Who would guess that something as unassuming as the Pim-800 could command so much attention in factories and work sites worldwide? Yet, there it is—making production lines hum, water treatment smooth, and chemistry labs safer. If you've ever watched liquids move almost magically between tanks, odds are a Pim-800 was doing the heavy lifting behind the scenes. This workhorse doesn't just move fluids. It keeps entire processes flowing, quite literally. Now, let's go deep into why the Pim-800 holds such a respected spot, what makes it tick, and how to get the most out of it, whether you’re a technician or just curious how stuff keeps running when it should.
Pim-800 Specifications and Core Features
The first thing most folks notice is how solid the Pim-800 feels. Built mostly from stainless steel with clever polymer reinforcement at stress points, it's engineered to shrug off all sorts of rough treatment. It's obvious the designers planned for days—and nights—where this pump just can't let you down. It's rated to handle up to 800 liters an hour, making it ideal for mid to large-scale jobs without tipping over into overkill mode.
Let's break down what really makes the Pim-800 tick. At its heart is a powerful asynchronous motor rated at 2.3 kW, with built-in thermal overload protection—so you’re not left with a melted mess if something jams. It operates smoothly at pressures up to 6 bar and can handle fluids up to 80°C (176°F) without complaining. And in terms of noise? The Pim-800 operates at under 60 decibels, so you won’t have to shout to be heard around it. Not bad for a powerhouse, right?
Compatibility is another big plus. The Pim-800’s connection ports are standard 1.5-inch NPT, making it plug-and-play for most setups without endless adapters. There’s also an integrated digital display for real-time performance readings. Here’s a quick overview of the tech specs you’ll want handy:
Feature | Spec |
---|---|
Flow Rate | Up to 800 L/hr |
Maximum Pressure | 6 Bar (87 PSI) |
Power | 2.3 kW |
Operating Temp | up to 80°C (176°F) |
Inlet/Outlet Size | 1.5 inch NPT |
Noise Level | < 60 dB |
Main Material | Stainless Steel/Polymer |
Whatever industry you’re in—be it water filtration, food processing or mild chemicals—the Pim-800’s materials hold up to aggressive fluids, meaning less downtime for you and your crew. It’s not quite indestructible, but it tries pretty hard.
Typical Uses and Real-World Scenarios
So where do you actually see the Pim-800 in action? You find it in water treatment facilities, keeping those purification processes smooth so your tap water doesn’t taste like a swimming pool. Food and beverage? The Pim-800 moves everything from syrups to sauces without introducing metal ions or anything funky into the mix. It’s even used in breweries—seriously, some of the tastiest craft beers hit your mug thanks to this pump’s gentle touch.
If you’ve ever visited a pharmaceutical workshop, chances are the Pim-800 hums away there too, circulating solutions in a sterile environment. Not a small feat, as it’s got to keep everything squeaky clean and contamination-free. In agriculture, the pump handles fertilizers and irrigation with zero drama, helping deliver nutrients evenly across fields or massive greenhouses. Its resistance to corrosion is huge here—the last thing you want is a rusty pump giving out halfway through growing season.
In one case I heard about, a medium-sized city upgraded its main water treatment pumps with Pim-800 units. Water flow reliability shot up almost instantly, and power bills actually dropped a bit thanks to how efficient these things are. One maintenance supervisor reported a five-year stint with minimal breakdowns—just routine swaps of seals and bearings. When you think about the scale—thousands relying on clear water daily—it’s wild how much hinges on a single pump.
For factories, efficiency matters. The Pim-800 shines with viscous fluids, making it a staple for chocolate and honey processors who need constant, gentle flow. It works equally well for more ‘hardcore’ jobs, like acid transfer, where resistance to chemical attack saves thousands in replacement costs each year. Here are some of the most frequent real-world applications:
- Municipal water and wastewater treatment
- Food and beverage handling (dairy, brewing, syrup transfer)
- Pharmaceutical production and sterile environments
- Printing and ink circulation lines
- Agricultural irrigation and fertilizer distribution
- Chemical transfer with moderate aggressiveness
So, if you see the Pim-800 tag on a piece of equipment next time you’re in a plant, you’re looking at a core player, not just another generic gadget.
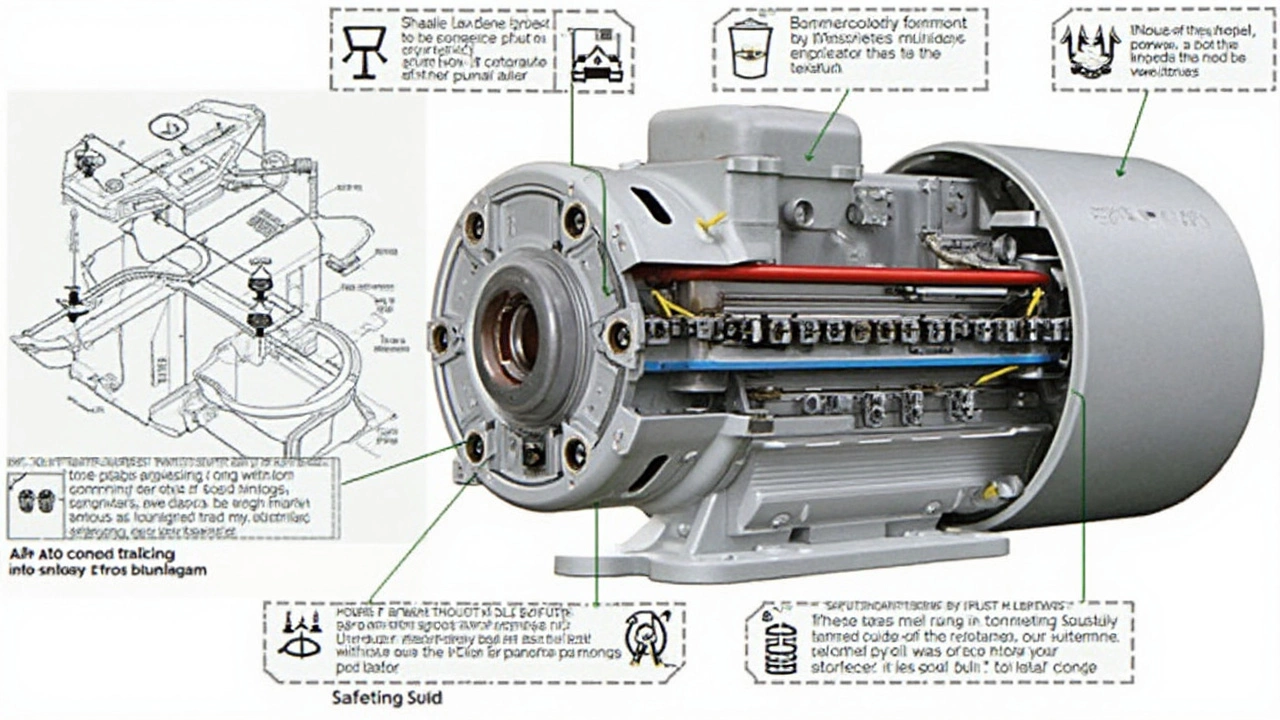
Maintenance, Troubleshooting, and Longevity Tips
No matter how tough the Pim-800 is, good maintenance keeps it from turning into a needless headache. Most issues come down to old seals, dirty filters or running dry for too long. An easy weekly check is to look for any leaks around the connection ports and listen for odd rattles. Don’t assume silence is golden—sometimes a pump gets so clogged it goes quiet. If the digital display flashes an error code, grab the manual or better yet, bookmark the manufacturer’s troubleshooting site for those quick fixes.
Seal swaps are the most regular fix, usually once or twice a year depending on usage. It’s as simple as shutting off the pump, depressurizing the lines, and using the provided kit to swap out the seal. No need to call in a specialist unless you’re facing complex fluids or unique setups. Impeller cleaning is worth tackling every couple of months, especially if you deal with sticky liquids or sediment. A soft brush and mild solvent will do, but remember—skip abrasives or you’ll risk a nicked blade and bigger headaches down the road.
One cool tip: install a clear inline filter before the pump inlet. You’ll catch debris before it chews up seals and impellers. Plus, it’s oddly satisfying to see all the gunk before it becomes a crisis. Temperature is also key. The Pim-800 doesn’t love being run for hours near its max temp. If you need that level of heat daily, stagger shifts or add a bypass system to keep things cooler. Temperature spikes over 80°C should set off alarms—ignore them and you may fry the winding insulation for good.
Best thing you can do? Log everything. Jot down run hours and conditions every week. Most issues are a slow creep, not a sudden blast. Your log will show patterns—like if seals wear down faster with a new fluid mix. And don’t forget the humble gasket. It’s cheap to replace but a disaster if ignored. Get a toolkit handy with spare O-rings, gaskets, and a backup thermal fuse; these parts cost less than a coffee but save hours of downtime.
Here’s a handy maintenance interval summary:
Task | Interval |
---|---|
Seal inspection/replacement | 6-12 months |
Filter cleaning/replacement | 1 month |
Impeller cleaning | 2-3 months |
Thermal sensor test | 6 months |
Main bearing lubrication | Annually |
Always keep an ear out for new noises, and resist the urge to push the Pim-800 way past its stated specs. It’ll work—but you’ll pay with shorter life. So it’s really about treating the gear with the respect you’d want for your favorite toolbox. The payoff is months or years of worry-free performance.
Safety, Upgrades, and Insider Advice
Even a solid pump like the Pim-800 can bite if you get slack with safety. First, always lock out power before doing any hands-on work. The capacitors in these motors can hold charge for a while even after unplugging. Ground faults are rare, but a wet floor and loose wire can light up your day in a bad way. If you’re running harsh chemicals, always double-check that the internal seals and housing are rated for your specific brew—just because it’s stainless steel doesn’t mean it’s invincible to every acid or alkali.
Personal protective equipment (PPE) isn’t just box-checking. Goggles, gloves and real work boots save toes and fingers. One overlooked move: always purge the lines of trapped pressure before disconnecting anything. A surprise jet of caustic fluid sure wakes you up, but the ER doctor might not see the fun in that.
If you want more out of your Pim-800, upgrades are everywhere. Smart modules can now tap into the digital port to send real-time performance stats right to your phone or facility dashboard. Predictive maintenance sensors track bearing wear, vibration, and temperature spikes way before you’d ever notice them by ear. It’s genuinely wild how much tech you can squeeze into something that still fits on a small bench.
Insider move? Befriend the distributor’s tech support. They’ve seen every weird install and issue you can imagine. A quick call or chat can shave days off troubleshooting. Also, watch for recall bulletins. There was a minor gasket batch flaw back in 2023—a wild two weeks for some users, but a solid reminder to register your product so you get those alerts fast.
Oh, and label each pump clearly with its intended service. Too many disasters start when someone swaps a unit set up for food with one that handled chemicals last week. Cross-contamination isn’t just gross—it’s dangerous. Keep a little laminated tag on each Pim-800 showing last service, what’s inside, and the right contact info if trouble hits.
For folks who want peak reliability, look into a backup Pim-800 on a "lead-lag" system. If the first pump flags or fails, its twin automatically picks up the slack—production keeps rolling and you get time to fix problems at your own pace. It sounds high-tech, but it’s pretty much plug, set, and forget with the right relays.
So yes, the Pim-800 isn’t glamorous, but it’s dead reliable and loaded with tricks for anyone willing to get hands-on. Give this pump some honest attention and it’ll pay you back every day you run it. Whether keeping a city’s water running or brewing your favorite beer, the Pim-800 carries its weight and then some.